About Combined Heat & Power
 |
While the traditional method of producing separate heat and power has a typical combined efficiency of 45%, CHP systems often have total efficiencies of 70-80% |
 |
CHP, also known as cogeneration, is the concurrent production of electricity or mechanical power and useful thermal energy (heating and/or cooling) from a single source of energy. CHP is a type of distributed generation, which, unlike central station generation, is located at or near the point of consumption. Instead of purchasing electricity from a local utility and then burning fuel in a furnace or boiler to produce thermal energy, consumers use CHP to provide these energy services in one energy-efficient step. CHP's inherent higher efficiency and the avoidance of transmission losses in the delivery of electricity from the central station power plant to the user result in reduced energy use and lower greenhouse gas (GHG) emissions.
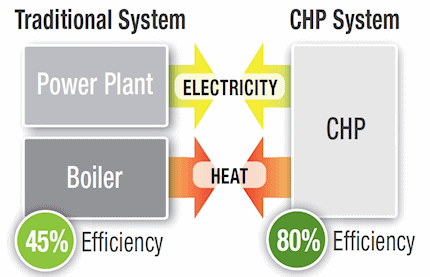
Every CHP application involves the recovery of otherwise-wasted thermal energy to produce useful cooling, heating, or process thermal energy or electricity. The most common CHP configuration is known as a topping cycle, where fuel is first used in a heat engine or prime mover to generate power, and the waste heat from the power generation equipment is then recovered to provide useful thermal energy to the site. As an example, a gas turbine or reciprocating engine generates electricity by burning fuel and then uses a heat recovery unit to capture useful thermal energy from the prime mover's exhaust stream and cooling system. Alternatively, steam turbines generate electricity using high-pressure steam from a fired boiler before sending lower pressure steam to an industrial process or district heating system. Waste heat streams can be used to generate power in what is called bottoming cycle CHP-often called waste-heat-to-power. In this configuration, fuel is first used to provide thermal energy to an industrial process, such as a furnace, and the waste heat from that process is then used to generate power.
CHP technology can be deployed quickly, cost-effectively, and with few geographic limitations. CHP can use a variety of fuels, both fossil - and renewable-based. It has been employed for many years, mostly in industrial, large commercial, and institutional applications. For optimal efficiency, topping cycle CHP systems typically are designed and sized to meet the users' thermal baseload demand.
CHP may not be widely recognized outside industrial, commercial, institutional, and utility circles, but it has quietly been providing highly efficient electricity and process heat to some of the most vital industries, largest employers, urban centers, and campuses in the United States. While the traditional method of separately producing usable heat and power has a typical combined efficiency of 45 percent, CHP systems can operate at efficiency levels as high as 80 percent.
The great majority of US electric generation does not make use of the waste heat. As a result, the average efficiency of utility generation has remained at roughly 34 percent since the 1960s. The energy lost in the United States from wasted heat in the power generation sector is greater than the total energy use of Japan. CHP captures this valuable wasted energy.
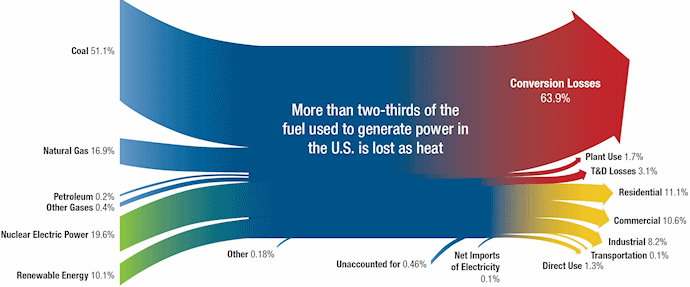
The United States currently has 85 gigawatts (GW) of CHP electric generating capacity installed, representing almost 9 percent of total generating capacity. This installed base of CHP generates about 505 million megawatt-hours (MWh) of electricity annually, or more than 12 percent of total electricity generated in the United States.
The size of CHP systems can range from 5 kW (the demand of a single-family home) to several hundred MW (the demand of a large petroleum-refining complex). For CHP systems to operate efficiently, a continuous thermal demand is required. This demand can be for laundry or pool-water heating in a hotel, space heating or cooling in a commercial office building, or material drying at a gypsum board factory. The type of thermal demand is unimportant, but must be present close to 24 hours a day for CHP systems to achieve the high efficiencies they are capable of.
CHP can be utilized in a variety of applications. Eighty-eight percent of US CHP capacity is found in industrial applications, providing power and steam to large industries such as chemicals, paper, refining, food processing, and metals manufacturing. CHP in commercial and institutional applications is currently 12 percent of existing capacity, providing power, heating, and cooling to hospitals, schools, campuses, nursing homes, hotels, and office and apartment complexes.