CHP Electric Technologies
CHP systems are integrated systems that consist of various components ranging from prime mover (heat engine), generator, and heat recovery, to electrical interconnection. CHP systems typically are identified by their prime movers or technology types, which include reciprocating engines, combustion or gas turbines, steam turbines, microturbines, and fuel cells. These prime movers are capable of consuming a variety of fuels, including natural gas, coal, oil, and alternative fuels, to produce shaft power or mechanical energy. Although mechanical energy from the prime mover is most often used to drive a generator to produce electricity, it can also be used to drive rotating equipment such as compressors, pumps, and fans. Thermal energy from the system can be used in direct process applications or indirectly to produce steam, hot water, hot air for drying, refrigeration, or chilled water for process cooling.
Reciprocating engines are by far the most numerous, but still not a majority, of the CHP prime movers. They are particularly well suited to small and medium applications, as they are cost-effective, readily available, fuel-flexible, and can achieve very high overall efficiencies. By capacity, combined cycle plants comprise just over half the CHP market. These plants typically are very large and serve industrial and utility customers.
Reciprocating Engines
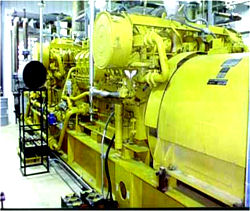
Courtesy: Cummins
Reciprocating internal combustion engines are the most widespread technology for power generation, commonly for small, portable generators to large industrial engines that power generators of several megawatts. Spark ignition engines for power generation generally use natural gas, though they can be set up to run on propane or landfill and biogas, and are available in sizes up to 5 MW. Reciprocating engines start quickly, follow load well, have good part-load efficiencies, and generally are highly reliable. In many instances, multiple reciprocating engine units can enhance plant capacity and availability. Reciprocating engines are well suited for applications that require hot water or low-pressure steam.
Appropriate for: CHP, Small District Energy
Further information:
- Reciprocating Engines chapter from the Catalogue of CHP Technologies (EPA CHP Partnership, PDF, 28 pgs)
- View a list of engine manufacturers and project developers on our Resources page.
Gas Turbines
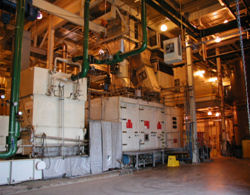
Courtesy: Metro Wastewater Reclamation District
Combustion or gas turbines are an established power generation technology available in sizes from several hundred kW to more than 100 MW. Gas turbines produce high-quality heat that can be used to generate steam for onsite use or for additional power generation (combined cycle). Gas turbines can be set up to burn natural gas, a variety of petroleum fuels, landfill or biogas, or can have dual-fuel capability. Gas turbines are well suited for CHP because their high-temperature exhaust can be used to generate process steam at conditions as high as 1,200 pounds per square inch gauge (psig) and 900 degrees Fahrenheit (°F). Much of the current US gas turbine-based CHP capacity consists of large combined-cycle CHP systems that maximize power production for sale to the grid while supplying steam to large industrial or commercial users. Simple-cycle CHP applications are common in smaller installations, typically less than 40 MW.
Appropriate for: Medium & Large CHP; District Energy
Further information:
- Gas Turbines chapter from the Catalogue of CHP Technologies (EPA CHP Partnership, PDF, 26 pgs)
- View a list of turbine manufacturers and project developers on our Resources page.
Steam Turbines
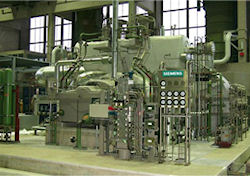
Courtesy: Siemens
Steam turbines generate electricity from the heat (steam) produced in a boiler, converting steam energy into shaft power. Steam turbines are one of the most versatile and oldest prime mover technologies used to drive a generator or mechanical machinery. The energy produced in the boiler is transferred to the turbine through high-pressure steam that in turn powers the turbine and generator. This separation of functions enables steam turbines to operate with a variety of fuels, including natural gas, solid waste, coal, wood, wood waste, and agricultural by-products. The capacity of commercially available steam turbines ranges from 50 kW to more than 250 MW. Ideal applications of steam turbine-based CHP systems include medium- and large-scale industrial or institutional facilities with high thermal loads, and where solid or waste fuels are readily available for boiler use.
Appropriate for: Large CHP; District Energy, Large Waste Heat Recovery
Further information:
- Steam Turbines chapter from the Catalogue of CHP Technologies (EPA CHP Partnership, PDF, 21 pgs)
- View a list of turbine manufacturers and project developers on our Resources page.
Microturbines
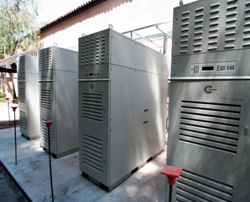
Courtesy: Capstone Turbine
Microturbines are very small combustion turbines with outputs of 30 kW to 300 kW. Microturbine technology has evolved from the technology used in automotive and truck turbochargers and auxiliary power units for airplanes and tanks. Microturbines are compact and lightweight, with few moving parts. Many designs are air-cooled and some even use air bearings, thereby eliminating the cooling water and lube oil systems. In CHP operation, a heat exchanger transfers thermal energy from the hot exhaust to a hot water or low-pressure steam system. Exhaust heat can be used for a number of different applications, including potable water heating, absorption chillers and desiccant dehumidification equipment, space heating, process heating, and other building uses.
Appropriate for: Small and Medium CHP
Further information:
- Microturbines chapter from the Catalogue of CHP Technologies (EPA CHP Partnership, PDF, 24 pgs)
- View a list of turbine manufacturers and project developers on our Resources page.
Fuel Cells
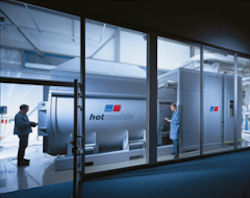
Courtesy: MTU
Fuel cells use an electrochemical or battery-like process to convert the chemical energy of hydrogen into water and electricity. In CHP applications, heat is generally recovered in the form of hot water or low-pressure steam (<30 psig), and the quality of heat depends on the type of fuel cell and its operating temperature. Fuel cells use hydrogen, which can be obtained from natural gas, coal gas, methanol, and other hydrocarbon fuels. Fuel cells promise higher efficiency than generation technologies based on heat engine prime movers. In addition, fuel cells are inherently quiet and extremely clean running. Like microturbines, fuel cells require power electronics to convert the direct current to 60-Hertz alternating current. Many fuel cell technologies are modular and capable of application in small commercial markets; other technology utilizes high temperatures in larger systems suited to industrial CHP applications.
Appropriate for: Small and Medium CHP
Further information:
- Fuel Cells chapter from the Catalogue of CHP Technologies (EPA CHP Partnership, PDF, 25 pgs)
- View a list of fuel cell manufacturers and project developers on our Resources page.