CHP Thermal Technologies
Each of the CHP prime mover technologies described in
the previous page produce excess heat that is recycled
for another thermal energy need, such as space heating,
domestic hot water, air conditioning, humidity control,
process steam for industrial steam loads, product
frying, greenhouses, or nearly any other thermal energy
need. The end result is significantly more efficient
than generating power, heating, and cooling separately.
Below are descriptions of some of the technologies that
run on the recycled thermal energy. Which one you employ
obviously depends on what output you need and on the
temperature and quantity of the excess heat available.
It is often possible to employ more than one of these,
either at the same time (i.e. air conditioning and
humidity control) or seasonally (i.e. cooling in the
summer and heating in the winter).
Efficient capture and effective use of thermal energy is
essential for maximizing the energy savings and economic
return of CHP. Cooling is often an especially-useful
add-on, as it allows customers to reduce seasonal peak
electric demand and allows future electric and gas grids
to operate with more level loads.
In most topping CHP
applications, the exhaust gas from the electric
generation equipment is ducted to a heat exchanger to
recover the thermal energy in the gas. Generally, these
heat exchangers are air-to-water heat exchangers, where
the exhaust gas flows over some form of tube and fin
heat exchange surface and the heat from the exhaust gas
is transferred to make hot water or steam. In the
majority of installations, a flapper damper or "diverter" is employed to vary flow across the heat
transfer surfaces of the heat exchanger to maintain a
specific design temperature of the hot water or steam
generation rate. The hot water or steam is then used to
provide hot water or steam heating and/or to operate
thermally activated equipment, such as an absorption
chiller for cooling or a desiccant dehumidifier for
dehumidification.
The next frontier in
thermally-activated technologies for CHP - especially
absorption chillers and desiccant dehumidifiers - is to
factory design pre-engineered, integrated, packaged
systems using standard, modular equipment, as opposed to
using custom-designed and custom-engineered systems for
each particular site. Some companies are making strides
in smaller-scale integrated systems (small, medium and
large commercial sites or small industrial sites);
larger sites will still require custom work.
Absorption Chillers
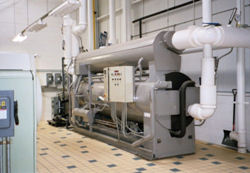
Courtesy: UTC / Carrier
All chillers use energy to remove heat from a
building. In the case of absorption chillers, the energy
comes from heat. (Yes, although this sounds
counterintuitive, they do use heat to produce cooling.)
This heat can be supplied by natural gas, steam, or
waste heat. This highly efficient technology uses less
energy than conventional chilling equipment, and also
cools buildings without the use of ozone-depleting
chlorofluorocarbons (CFCs).
Absorption chillers work by transferring the thermal
energy from a heat source to a heat sink through an
absorbent fluid and a refrigerant. The absorption
chiller creates a refrigerative effect by absorbing and
then releasing water vapor into and out of a lithium
bromide solution (see figure below).
Simplified Absorption Cycle
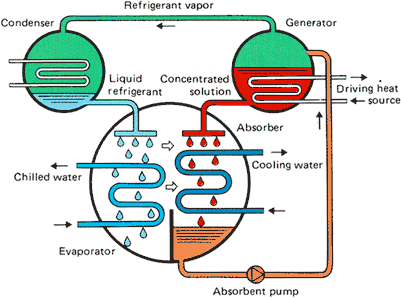
Ammonia Absorption Chillers
Ammonia-based absorption chillers use a mixture of
ammonia and water as a working pair, with ammonia as the
refrigerant, rather than the lithium-bromide and water
used in regular absorption chillers. Ammonia absorption
chillers are used in a range of applications, from small
refrigerators of less than 25 refrigeration tons (RT) of
cooling capacity to mammoth heat-recovery machines
installed with power plants.
Ammonia is an excellent refrigerant with a high
latent heat and excellent heat transfer characteristics.
Compared to regular lithium bromide absorption chillers,
ammonia absorption chillers are suited for certain
industrial applications that require extremely cold
temperatures (below 32 degrees F or 0 degrees C, where
the water in lithium bromide systems freezes).
Because of its toxicity, ammonia absorption chillers
are often restricted to applications in which the
equipment is outdoors to allow natural dilution of any
leaks.
Ammonia absorption chillers are most commonly found
at large-scale food processing, petrochemical, and
fertilizer plants. However, they are also newly
available for residential and light commercial
applications, generally in the range of 2 to 10 RT,
which could be modularized into larger systems.
Desiccant Dehumidifiers
Desiccants can be used to remove humidity from air.
In humid climates, this reduces the cost of air
conditioning and improves indoor air quality. Space
conditioning is comprised of two separate components:
- Sensible cooling - lowering the air temperature
- Latent cooling - reducing humidity in the air
By reducing moisture content of the air, desiccants
reduce the latent cooling load on conventional AC
equipment. Thus, the chiller load is primarily limited
to only the sensible cooling (i.e., reducing the
temperature). By dehumidifying the air, desiccants
improve the efficiency of standard air conditioning
equipment and thereby lower the cost for air
conditioning. Controlling humidity (to less than 60%)
helps prevent the growth of mold, bacteria, and
microorganisms that cause allergies or are otherwise
harmful to human health.
Desiccants either chemically or physically bond water
vapor to hydroscopic materials. Once the dessicant
material is saturated, it can be dried out using hot
exhaust from a CHP system, and used again and again.
Heat is required to remove water from the desiccant,
thereby regenerating it to be reused for further
dehumidification. Thus, desiccants are an excellent use
of the heat from CHP systems throughout the cooling
season.
Heat Recovery Steam Generators
Heat Recovery Steam Generators (or "HRSG," often
pronounced "herzig") are essentially boilers that
capture or recover the exhaust of a prime mover such as
a combustion turbine, natural gas or diesel engine to
create steam.
The system consists of a bank of tubes that is
mounted between the prime mover and the exhaust stack.
Exhaust gases at temperatures of 800˚F to 1200˚F heat
these tubes. Water is then pumped and circulated through
the tubes and can be held under high pressure to
temperatures of 370˚F or higher resulting in the
production of high pressure steam. Since the flue gas
never comes in direct contact with the water, the steam
can be safely used in thermally activated cooling
equipment.
HRSGs, which range from 10-250 megawatts and have an
efficiency of 60-85%, are typically found in many
combined cycle power plants.
Heat recovery from a reciprocating engine is much
more complicated than with a gas turbine due to the
number of different heat streams that need to be tapped,
as shown in the figure below.
Heat Streams from a Reciprocating Engine
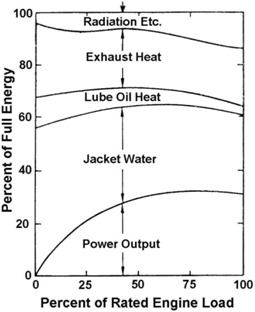
Heat from the jacket water, lube oil and exhaust can
all be captured, but not directly. The figure below
shows a very typical heat recovery configuration for a
reciprocating engine CHP application. The recovered heat
for a reciprocating engine takes the form of
low-pressure steam or hot water in all but the largest
units. It should also be noted that the heat from the
jacket water and cooling water must be ejected even if
it is not being used, so often reciprocating engine sets
will be equipped with a cooling tower to eject excess
heat.
Typical Reciprocating Engine CHP Configuration
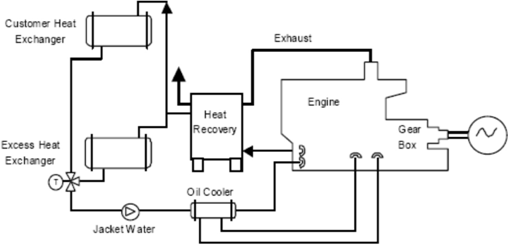